In this topic, you will learn the basic principles of DVM and how to convert a working
schematic to run in DVM. After converting your schematic to run in DVM, you will run a few
tests out of a built-in testplan on your schematic. Finally an introduction to testplan
syntax will be covered.
To download the examples for the Applications Module, click Applications_Examples.zip
Key Concepts
This topic addresses the following key concepts:
Schematic Prepared for DVM:
- To use DVM you need a schematic and a Testplan. Built-in testplans for
common converters, such as a DC/DC converter with a single input and output are
included in DVM.
- DVM uses special DC Input Sources, AC Line Input Sources, and Output Load symbols
where the electrical subcircuit used in the simulation can be changed for each
test in the testplan.
- The 3 and 4 pin output load subcircuits include the AC perturbation source for a
Bode Plot analysis.
- DVM keeps track of these special source and load symbols with a system of Managed Sources and Loads, where the source and
load reference designators are stored on the control symbol.
- When using symbolic values, the schematic stores the numerical values on the
DVM Control
Symbol and the testplan refers to those values using symbolic
references.
Testplans:
- Testplans are nothing but tab-delimited ASCII text files which you edit in a
spreadsheet program.
- Each row in a testplan is a test to be executed, each column defines an action
for that test.
- Testplans can use Symbolic Values to
represent the input voltage or output load levels, which greatly simplify the
reuse between schematic designs.
- Objectives are predefined
test configurations which define:
- The source and load subcircuits.
- The analysis type, e.g. Transient, POP, AC.
- The post-simulation measurements to be make as well as any additional
curves to create.
- Scalar measurements
made by DVM can be selected on the DVM Control Symbol
dialog.
What You Will Learn
In this topic, you will learn the following:
- How to configure a schematic for DVM.
- How to run tests from a built-in testplan on your schematic.
- The basics of testplan syntax.
Part I: Preparing the Schematic for DVM
At the very minimum, preparing a schematic for DVM requires you add a DVM control
symbol. There are two types of DVM Control Symbols: basic and Full Power
Assist. The basic control symbol enables a limited portion of DVM, and for the
exercises in this topic, you will use the more flexible "Full Power Assist Control
Symbol." The Full Power Assist Control Symbol allows you to store Symbolic Values for the input voltage range or full
load current, which are required to run the built-in
testplans.
In this course you will modify built-in testplans and use the built-in
test objectives to setup a test suite.
In order to use the symbolic values, built-in testplans and test objectives, your
schematic requires:
- A Full Power Assist DVM Control Symbol.
- A DVM input source and an output load symbol.
- You enter the design specifications for the input voltage and output load into
the DVM control symbol.
In the next four short exercises, you will add source and load symbols to a
schematic, then add a control symbol and edit the circuit specifications for your
design.
Exercise #1: Add an Input Source Symbol
To add the input source, follow these steps:
- Open the apps_d_0_llc_converter_efficiency.sxsch.
- Delete the DC voltage source VIN on the left side of the schematic.
- From the parts selector, choose , and place the symbol where you removed the DC source
VIN.
- Add and remove wires to connect the source as shown below:
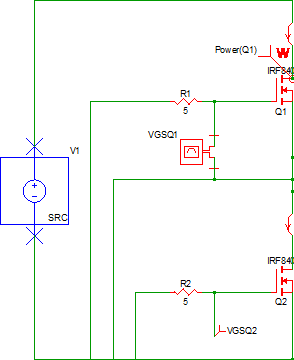
Exercise #2: Add a 3-Terminal Output Load Symbol
The 3 and 4-terminal DVM output loads have a SENSE (3-terminal) or a differential
SENSE (4-terminal) connection. These extra pins allow DVM to include the injected AC
perturbation source and Bode plot probe that are required for closed-loop AC
analysis. DVM automatically inserts these components into the load subcircuit
definition for the Bode plot tests. For this circuit you will use the 3-terminal
output load.
To add the 3-terminal output load, follow these steps:
- Delete the RL resistor and VAC source from the right side of the
schematic.
- From the parts selector, choose , and place it where you removed the load resistor RL. You will need
to mirror the symbol about the vertical axis using the F6 key before
placing the symbol.
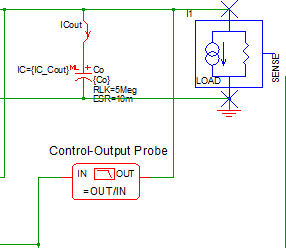
- Connect the SENSE terminal on the DVM 3-terminal output load to the
feedback network.
Note: The SENSE terminal provides the output voltage feedback
information to the converter control loop. During Bode plot tests, the small
signal AC source is inserted between the positive load terminal and the SENSE
terminal and perturbs the control loop. For all other test objectives, the
SENSE terminal is shorted to the positive output terminal of the load. The
schematic should appear as shown below:
Exercise #3: Add the DVM Control Symbol
The Full Power Assist DVM Control Symbol stores information about the circuit,
including specifications for the input voltage range and the full load output
current. It also stores analysis and timing information used to setup DVM
tests.
Note: The DVM Control Symbols are not electrically active, that is, there is
no netlist entry for the symbol. The DVM Control Symbol can be thought of as a
library of information about your circuit. When DVM needs to know some parameter
value, such as the full load current, it goes to the DVM Control Symbol to get the
information.
To place a DVM control symbol, follow these steps:
- From the parts selector, choose .
- Place the symbol at the top of the schematic.
Note: The program automatically detects the input source and output load, and adds the
reference designators to properties on the DVM Control Symbol.
It is important to note that when you place the DVM Control Symbol after placing the
source and load symbols, DVM performs a number of housekeeping tasks. These
include:
- DVM detects the input source and output load symbol(s) and configures the DVM
Control Symbol accordingly. DVM supports up to five input sources and six output
loads. You can add loads or sources at any time.
- DVM automatically reads the analysis parameters from the F11 window and adds
these parameters to the DVM Control Symbol.
Exercise #4: Enter Circuit Specifications
When you placed the DVM Control Symbol, the program detected the input source and
output load symbols and configured the control symbol with one managed input source
(V1) and one managed output load (I1). The program also read in the
analysis directives you set in the dialog, these directives were copied onto the control symbol. Since
the program has no way of knowing what the input and output voltages and load
currents are, you need to change these parameters to suit this particular circuit.
To change the circuit specifications, follow these steps:
- Double click on the DVM control symbol.
Result: The
SIMetrix/SIMPLIS DVM Control Panel opens.
- On the Circuit Specifications page, set the values as listed in the following
table.
Parameter |
Value |
Units |
Circuit Name |
test_llc_converter |
|
Circuit
Description |
LLC Converter |
|
Switching
Frequency |
85k |
Hz |
Note: Leave the default values for the other fields on this page.
- Click on DC Input in the page-selection box on the left side of the
control panel, and then enter the values listed below.
Parameter |
Value |
Units |
Voltage
|
Nominal |
380 |
V |
Minimum |
360 |
V |
Maximum |
400 |
V |
Misc.
|
Source
Resistance |
0 |
Ohm |
- Click on Output in the page-selection box, and enter the values listed
below.
Parameter |
Value |
Units |
Voltage
|
Nominal |
24 |
V |
Tolerances
|
Peak to Peak |
120 |
mV |
Current
|
Maximum |
5 |
A |
Light Load
|
@ Vin Min |
0.5 |
A |
@ Vin Max |
0.5 |
A |
Note: Leave the default values for the other fields on this
page.
- Click on the POP Analysis entry to bring up the POP page.
- Verify that Use "Pop Trigger" schematic device is checked.
- Click Ok to save the specification changes.
- Save the schematic as test_llc_converter.sxsch.
Result: At this point, the schematic is configured to run the
built-in testplans which use symbolic values and the DVM source and load
subcircuits. A per-prepared schematic at this state is included in the zip
archive with file name:
apps_d_1_llc_converter_efficiency.sxsch.
Part II: Run a Built-in Testplan
Now that you have prepared the schematic for DVM, you can run a built-in testplan on it.
In the next exercise, you will run a Bode Plot test from the built-in testplan at
nominal input voltage and 100% load.
Exercise #5: Run a Bode Plot Test
- Open the test_llc_converter.sxsch schematic you created in Exercise #4, or the
apps_d_1_llc_converter_efficiency.sxsch schematic from the zip archive,
if you didn't complete the previous exercise.
- Run the built-in DC/DC 1 Input/1 Output testplan using the menu:
Result: A test selection dialog
appears as follows:
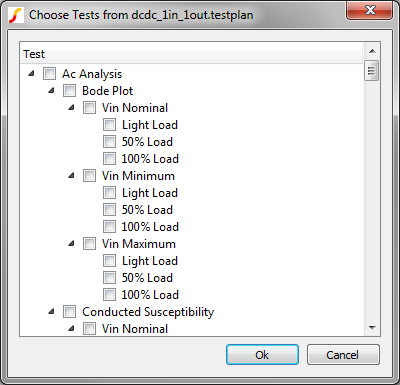
- Select the third test - AC Analysis > Bode Plot > Vin Nominal > 100%
Load
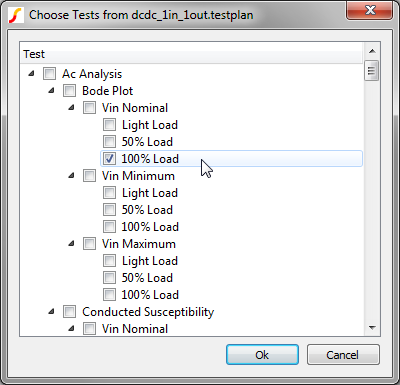
- Click Ok
Result: DVM configures the schematic
for a Bode Plot test, which includes:
- Setting a POP and AC analysis for the simulation run.
- Configuring the input source to be a DC source.
- Configuring the output load to be a Bode Plot type load which includes
loop perturbation and a Bode Plot probe.
- Applying the measurements to the input source and output load. The load
measurements include gain crossover frequency, gain margin and phase
margin.
This simple exercise demonstrates the steps DVM makes to setup the schematic for
simulation, simulate the design, and gather the results. Of course, you could have
selected multiple tests and DVM would process the tests in order, taking the same steps
for each test you selected. The actions performed for a test are defined in the testplan
row for the test, and in the next part, you will learn the testplan format for this
test.
Part III: All About Testplans
In the Key Concepts section you learned that to run DVM, you need a prepared schematic
and a testplan to run on that schematic. In Part I you prepared your schematic for DVM,
and in Part II you ran a test without really looking into what is inside the testplan.
In this section, you will learn about testplan syntax, and how to edit testplans.
Exercise #6: View Built-in Testplan
In the previous exercise, you ran a single test out of the DC/DC (1-input,
1-output) testplan. When you ran that testplan, a copy of the testplan was
made and saved to your schematic's working directory. You can now use this copy as a
template or a starting point for defining custom tests. To open this copy in
Microsoft Excel,
- Open Microsoft Excel.
- On the test_llc_converter_efficiency.sxsch schematic, right click on the
gray title bar where the filename is displayed in bold.
Result: The following context menu is displayed:

- Select the Open containing folder menu item.
Result: A Windows Explorer window opens in the schematic's
directory, Applications_Examples.
- In the Windows Explorer window, scroll down to the
dvm_builtin-dcdc_1in_1out.testplan file.
- Drag and drop this file into Excel.
- You may be presented with an import wizard dialog. If so, select tab delimited
and click Ok on the other import dialog pages.
Testplan files are tab-separated text files with a .testplan extension
which define the tests to be run. Testplans have the following rules:
- Blank lines are ignored.
- Lines starting with an asterisk (*) are considered comments and are ignored.
- Inline comments are not supported; that is, you can comment out an entire line, but not
a portion of a line.
- Each non-blank, non-comment line in the testplan describes a set of test conditions for
a single test. Each column performs some action during the test.
- The testplan can have a header row. The first entry on the header row starts with
*?@. The program reads the file and identified the header row by looking for this
special three character sequence.
- Any column can have an empty cell in a row but the behavior is different for columns
with function headings.
- If the column heading is a function, such as
Var(vout , 1.2), DVM uses the default value, in this case
1.2.
- If the column heading is
not
a function, DVM makes no changes for that column where a cell is empty.
The header row for this testplan is on row #4, and the Bode Plot test with the input
voltage at the Nominal value and the load set to 100% is on row #8.
1 |
|
*** |
2
|
|
***
dcdc_1in_1out.testplan |
3
|
|
*** |
4 |
|
*?@ Analysis |
Objective |
Source |
Load |
Label |
5
|
|
*** |
6
|
|
Ac |
BodePlot(OUTPUT:1) |
Source(INPUT:1,
Nominal) |
Load(OUTPUT:1, Light) |
Ac|Bode Plot|Vin Nominal|Light
Load |
7
|
|
Ac |
BodePlot(OUTPUT:1) |
Source(INPUT:1,
Nominal) |
Load(OUTPUT:1, 50%) |
Ac|Bode Plot|Vin Nominal|50%
Load |
8
|
|
Ac |
BodePlot(OUTPUT:1) |
Source(INPUT:1,
Nominal) |
Load(OUTPUT:1, 100%) |
Ac|Bode Plot|Vin Nominal|100%
Load |
9 |
|
*** |
Let's examine the testplan row by row and then column by column. The first three rows
are comments and are completely optional.
Comment Rows
1 |
|
*** |
2
|
|
***
dcdc_1in_1out.testplan |
3
|
|
*** |
As long as the first character in the line is a *, you may change the text in
these line without affecting DVM operation.
The Header Row
The next row is the extremely important header row. The header row tells the program
what type of entries to expect in fields for the following rows. It is assumed that
all electrical tests are entered below the header row. Here is the header row and we
will examine this in more detail:
4 |
|
*?@ analysis |
objective |
source |
load |
label |
- The first entry:
*?@ analysis
The Analysis column allows you to either explicitly
set a simulation analysis (.POP. .TRAN, etc) or in this case the Ac placeholder is
used. This column is not strictly needed for the built-in testplans.
- The second entry:
objective
tells the program to expect one
of the predefined test
objectives. In this example, a BodePlot() Test Objective which measures the loop response of the
circuit.
- The third entry:
source
can be used to modify subcircuit
type used for a source, or to set the amplitude of a source.
- The fourth entry:
load
like the source column, you can
change the subcircuit type for a load or change the load value with this
column.
- The fifth column is the test Label. The
label is electrically inactive and is used to populate the test selection
dialog.
A couple of comments are in order and some conclusions can be made from this testplan
header row.
The Vin Nominal, 100% Load Bode Plot Test
Now that you know the purpose of the header row, you will learn what actions are
performed for each field entry for the test you just ran, the nominal input voltage,
100% load Bode Plot test. In the table below, the header row and the Bode Plot test
row are duplicated for clarity.
4 |
|
*?@ Analysis |
Objective |
Source |
Load |
Label |
8
|
|
Ac |
BodePlot(OUTPUT:1) |
Source(INPUT:1,
Nominal) |
Load(OUTPUT:1,
100%) |
Ac|Bode Plot|Vin
Nominal|100% Load |
- The first entry:
Ac
is a placeholder, and tells DVM to
expect a valid AC test ojective in a following Objective entry.
- The second entry:
BodePlot(OUTPUT:1)
tells the program to
run a Bode Plot test on the symbolic reference designator OUTPUT:1. This
actual reference designator (I1) is stored on the DVM control symbol.
OUTPUT:1 literally means "Find the first output load reference
designator on the DVM Control Symbol and substitute that reference designator
here." The test objective does most of the work for this test. The BodePlot() Test Objective performs these actions:
- Sets up a POP and AC analysis for the circuit. The simulation parameter
values are taken from the DVM Control Symbol.
- Configures the input source to be a DC Input Source.
- Configures the output load to be a Bode Plot Load - Resistive Load, and this
load contains the AC perturbation source and Bode Plot probe.
- Sets up the measurements for the Bode Plot test, you elect which
measurements to make on the input sources, output loads, and the AC Bode
Plot curves in the DVM Measurements
dialogs. These measurements are stored on the DVM Control Symbol.
- Finally, the BodePlot() test objective sets the specification checking for
the test. For the Bode Plot test, there are two specifications - Gain
Margin, and Phase Margin. You define both specification values on the DVM
Control Symbol.
- The third entry:
Source(INPUT:1, Nominal)
uses the
INPUT:1 symbolic reference designator, and this entry does only one
thing: it changes the amplitude of the first managed source. The symbolic value
Nominal is read from the DVM Control Symbol. It should be noted that the
Source() Function doesn't change the
subcircuit type - that was changed by the test objective in a previous
column.
- The fourth entry:
Load(OUTPUT:1, 100%)
like the source
column, this entry changes the load current, in this case, the Load function
changes the value of the load to 100% of the full nominal load current. You set
the full load current on the DVM Control Symbol for each output.
- The fifth entry:
Ac|Bode Plot|Vin Nominal|100% Load
defines
how the test will be displayed in the test selection dialog. The pipe(|)
characters define levels of hierarchy in the test selection dialog: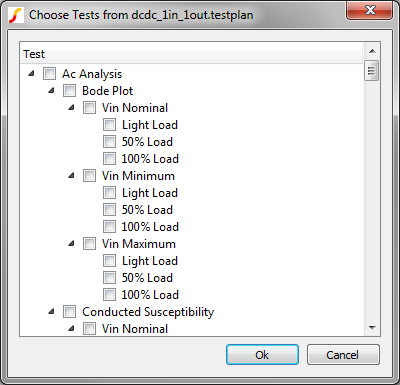
In this section you learned how the header row works in combination with a row which
defines a single test. In the next section, an animated slideshow describes the test
actions on a column-by-column basis for this particular test.
DVM Slideshow
The following slideshow illustrates the
sequence of actions that DVM takes as it executes a single test from the Built-In Sync Buck
testplan. The test used for this example is the same BodePlot test described in the previous
section.
- You can pause the slideshow by moving the mouse cursor over the images.
- To go forward or back one slide, click the arrow links that appear when you mouse over
the slideshow.
- Each slide number is shown in the bottom right-hand corner. You can jump to a particular
slide by clicking one of the gray squares at the bottom on the image. The current slide is
indicated by the white square.
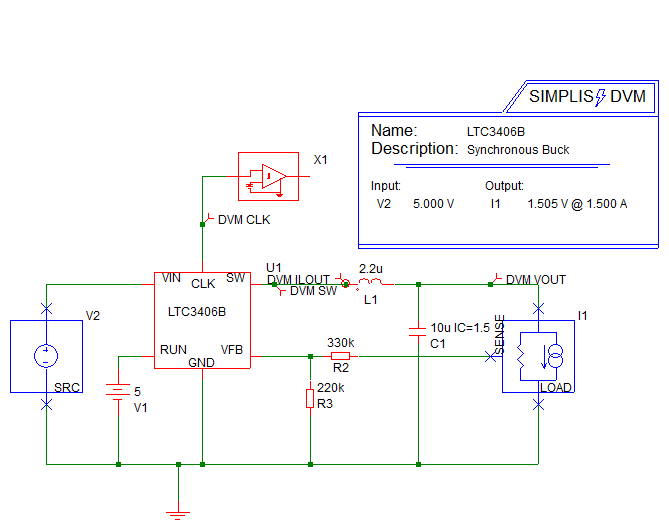
1 of 13
Schematic Configured
for DVM
Configuration
Includes:
- DVM Input Source Symbol
- DVM Output Load Symbol
- DVM Control Symbol
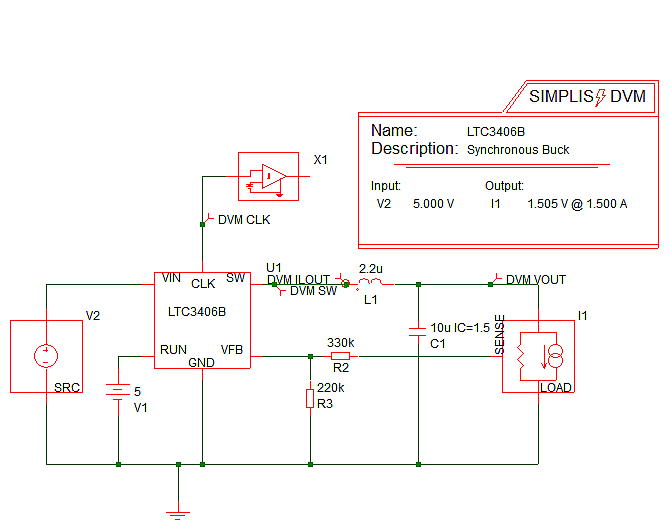
2 of 13
Run Built-In Sync
Buck Testplan
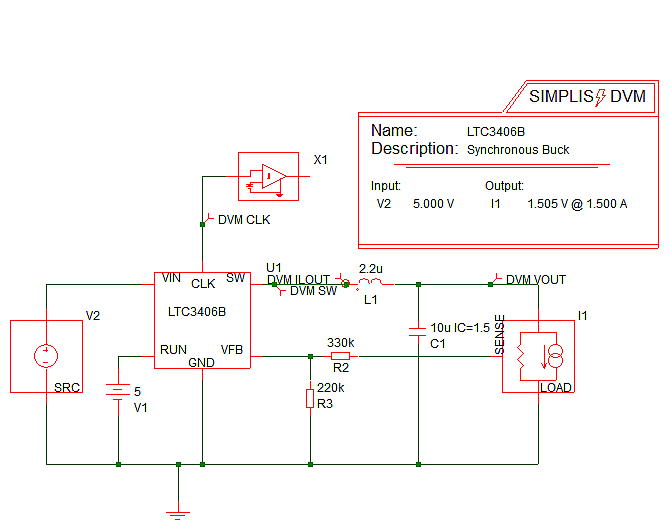
3 of 13
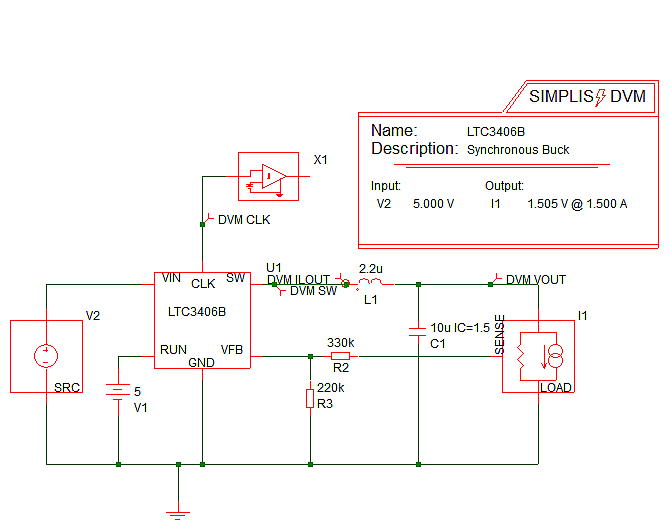
4 of 13
DVM Processes the Test Row:
Ac = AC Test Objective
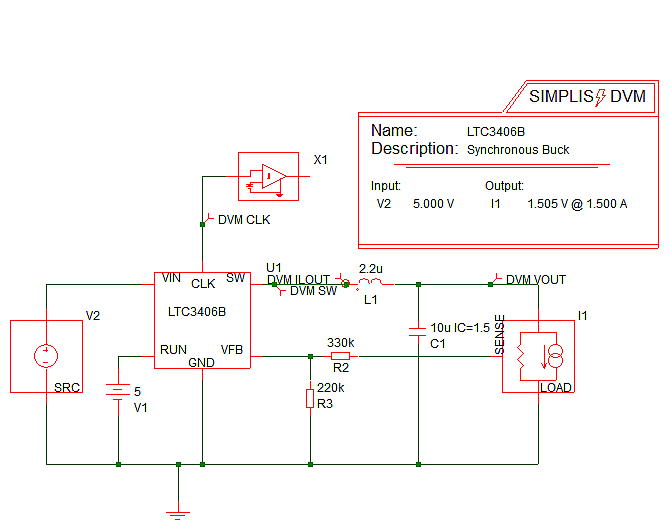
5 of 13
BodePlot()
Configures DC source
Objective |
BodePlot(OUTPUT:1) |
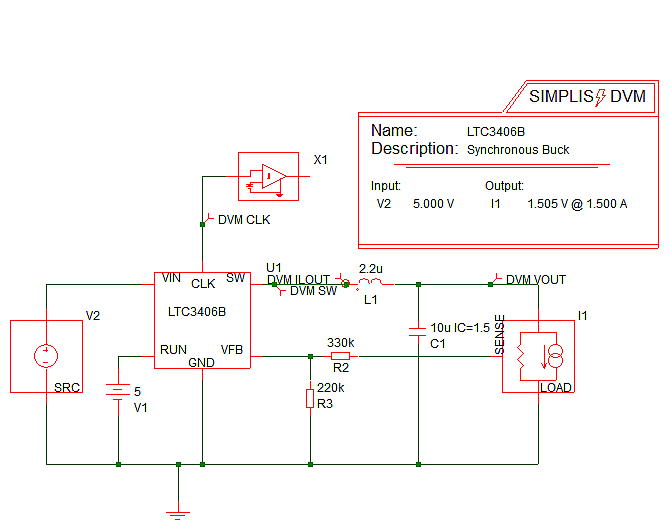
6 of 13
BodePlot()
Configures Bode-Type Load
Objective |
BodePlot(OUTPUT:1) |
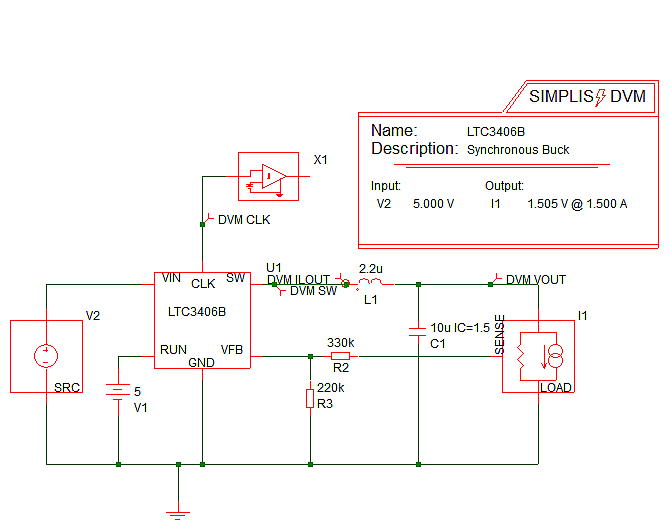
7 of 13
BodePlot()
Sets Analysis Directive
Objective |
BodePlot(OUTPUT:1) |
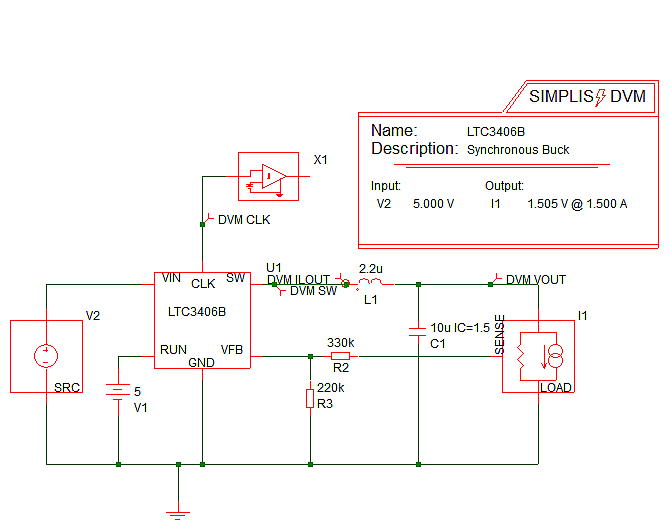
8 of 13
Source |
Source(INPUT:1, Nominal) |
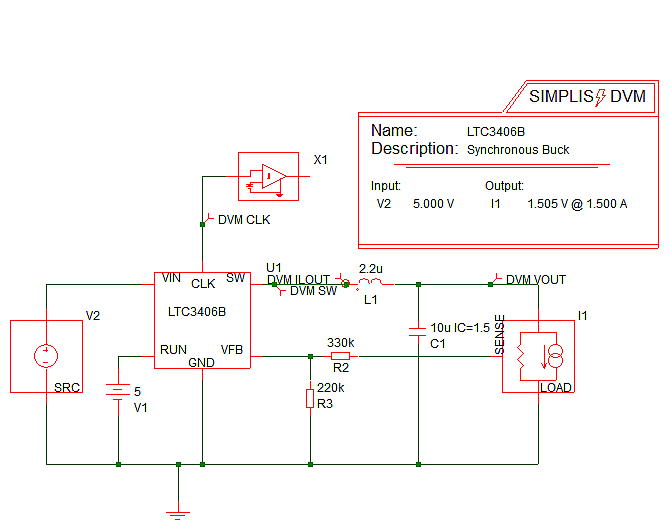
9 of 13
Set the load to 100% of the full load value
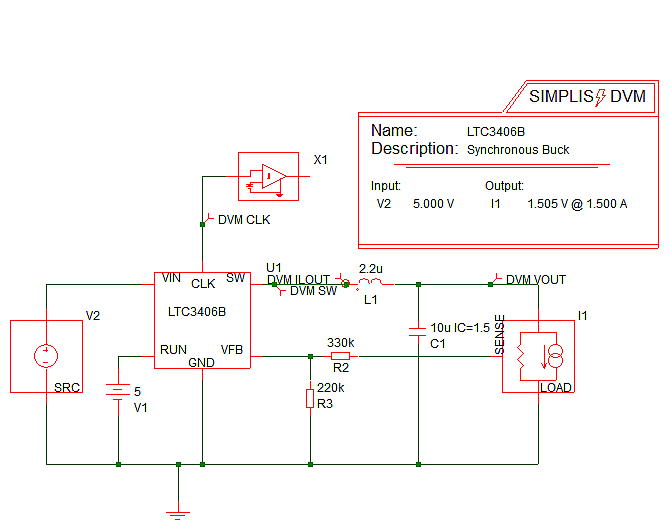
10 of 13
Label
Configures the Test Selection Dialog
Label |
Ac|BodePlot|Vin Nominal|100% Load |
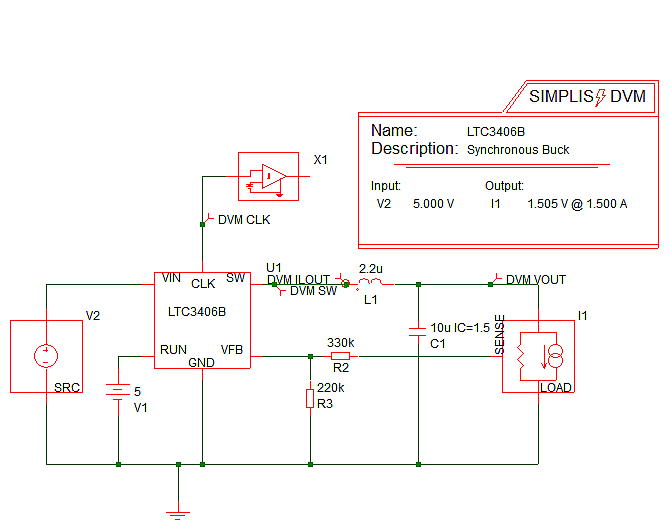
11 of 13
After
Configuring the Schematic,
DVM Launches the Simulation
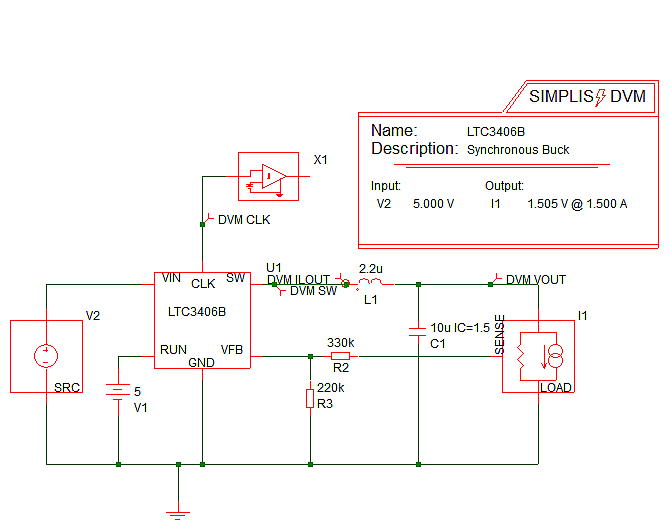
12 of 13
DVM
Collects Graph Data,
Measures Scalars,
Compares Scalars to Specifications
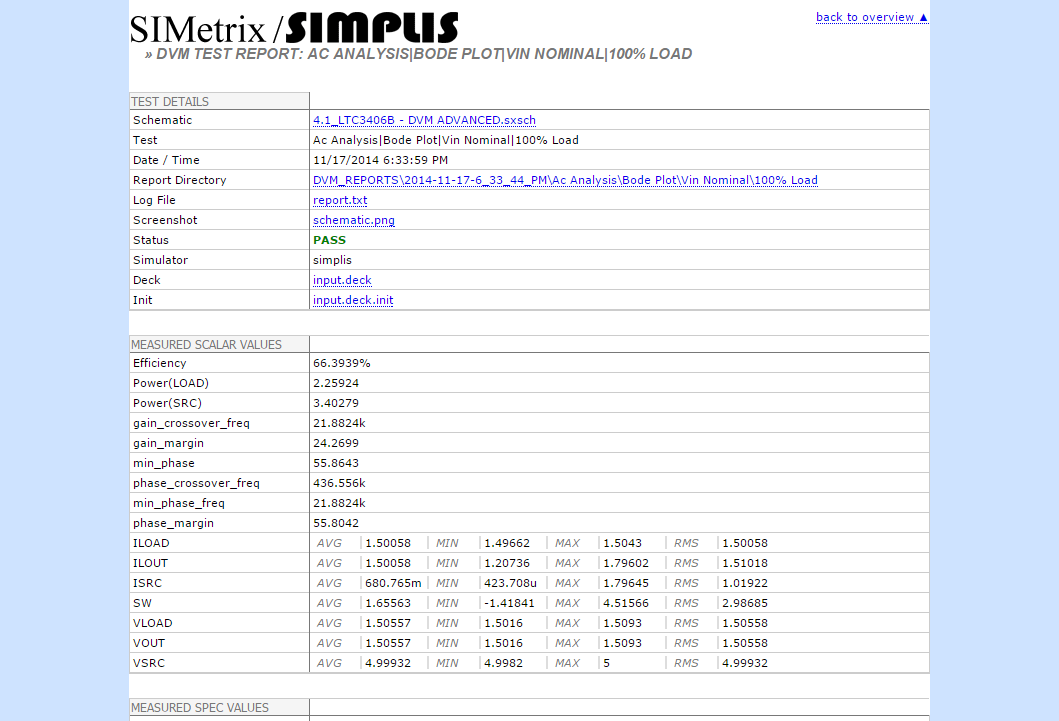
13 of 13
After
all Tests Complete,
the Test Report Opens
Although the slideshow illustrates actions
that DVM takes for a single test from the built-in testplan, the DVM functionality
encompasses much more than just Bode plot testing. Built-in testplans for one-input,
one-output and one-input, two-output DC/DC converters are provided and include a full suite
of tests that designers often run on power supplies, including Step Line, Step Load, Input
and Output Impedance, and more.
Additionally a full suite of AC/DC tests are
available in the one-input, one-output and thee-input, one-output Built-In AC/DC
testplans.
For a full list of available tests, see the
the following topics:
DVM also provides the ability to customize
testplans to suit any design. For details about how to customize test plans, see Customizing
Testplans in the DVM Tutorial.
Part IV: Symbolic Values
Note a very interesting fact about the DVM slideshow versus the LLC example you prepared
for and ran in DVM. The testplan is identical for both converters, yet the converter in
the slideshow has a 5V nominal input voltage while the LLC converter has a 380V nominal
input voltage. This is one place where the symbolic values for the input voltage sources
and the output loads really shines. By storing these specification values on the DVM
Control Symbol, instead of in the testplan, a single testplan can be used for both
converters.
In the next topic : Generating Efficiency Plots with Multi-Step Runs in DVM, you will explore a few
other testplan entries and see how small changes to a testplan yield dramatic results.
Conclusions and Key Points to Remember
- Using DVM requires a schematic prepared for DVM, and a testplan defining the tests
to be run.
- DVM can use symbolic values which are stored on the DVM control symbol.
- Testplans are simple tab delimited text files which you edit with a spreadsheet
program.
- The header row defines the allowed entries in each test row - that is, the allowed
column entries are defined by the header row entry for that column.